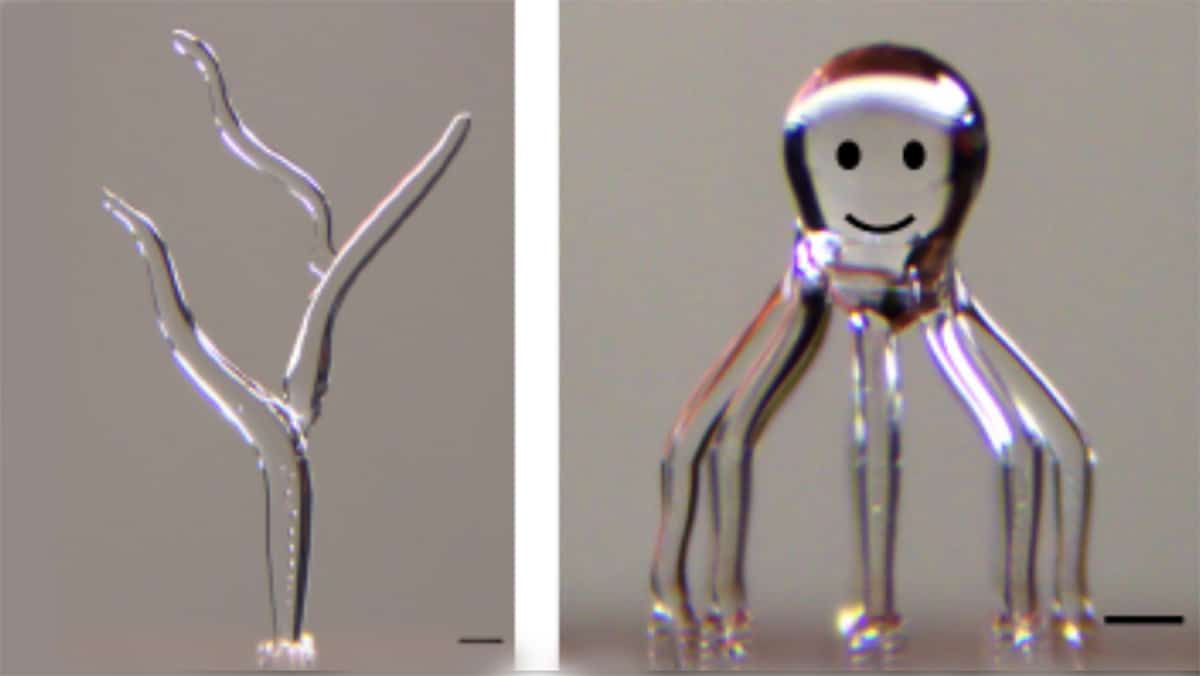
Water is the primary building block of any organism and the most abundant substance on the earth’s surface. Water’s rapid phase-change ability, along with its environmental and biological capability, also makes it a unique structural material for 3D printing of ice structures reproducibly and accurately.
Researchers at Carnegie Mellon University have introduced the freeform 3D printing (3D-ICE) process for high-speed and reproducible fabrication of ice structures with micro-scale resolution. This approach of 3D printing ice structure can be used to create sacrificial templates that later form the conduits and other open features inside fabricated parts.
“Using our 3D ice process, we can fabricate microscale ice templates with smooth walls and branched structures with smooth transitions. These can subsequently be used to fabricate microscale parts with well-defined internal voids,” said Akash Garg, a Ph.D. student in mechanical engineering.
The team uses the printed ice structures as sacrificial templates for “reverse molding” or inside-out 3D printing. The ice structures are submerged into the liquid or gel form of a chilled structural material, such as resin. After the material sets or is cured, the water is removed. For this purpose, the ice can be melted to evacuate the water. Alternatively, the ice can be sublimated by converting it into water vapor without turning it into liquid water. This ability to easily sublimate the ice allows for easy and “gentle” removal after casting and solidifying the surrounding structural material.
A high-resolution 3D printing system is used to deposit water droplets onto a -35 ◦C custom-built temperature-controlled platform that rapidly transforms the water into ice. The new process enables the printing of branched geometries with smooth surfaces and continuous variations in diameter with smooth transitions by modulating the ejection frequency of the water droplets and synchronizing it with the movements of the stage.
The researchers demonstrate this by printing multiple complex ice geometries, such as a tree, a helix around a pole, and even a one-and-a-half-millimeter tall octopus figurine. The rapid phase change of the water and the strength of the ice enabled freeform 3D printing of ice structures without requiring time-consuming layer-by-layer printing or support structures.
Experimental studies were performed to determine the printing path, motion-stage speed, and droplet frequencies to reproducibly fabricate smooth ice structures with straight, inclined, branching, and hierarchical geometries. These microscale ice structures can be used in biomedical engineering, advanced manufacturing, and possibly in art.
“Controlling so many parameters was challenging. We gradually built up in complexity,” explained Garg. “This is an amazing accomplishment that will bring exciting advances,” commented Ozdoganlar. “We believe this approach has enormous potential to revolutionize tissue engineering and other fields, where miniature structures with complex channels are demanded, such as for microfluidics and soft-robotics.”
Researchers 3D print tiny microscale ice structures
Source: Tambay News
0 Comments