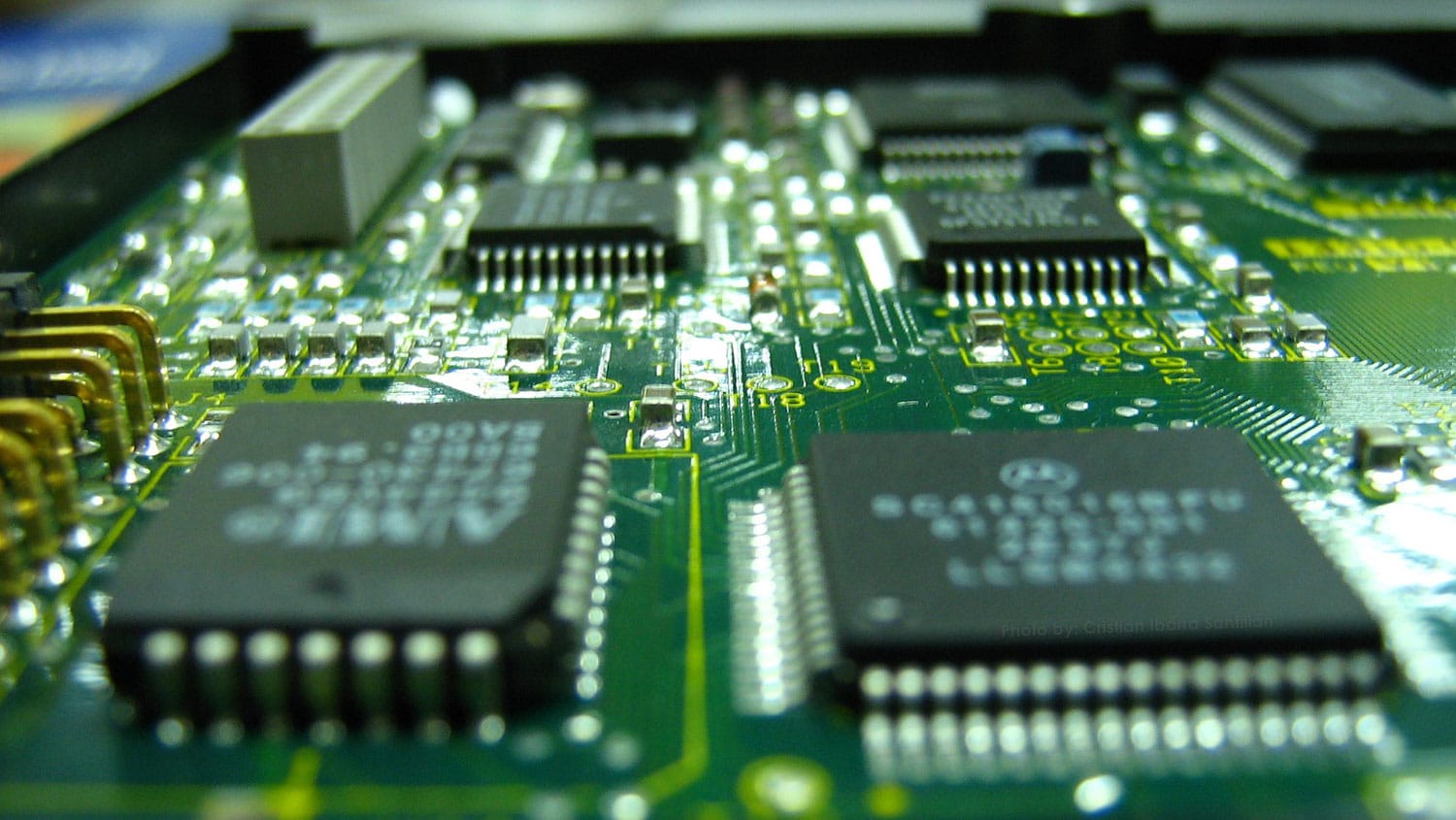
All electronic devices and circuitry generate excess heat. In order to avoid thermal-induced damage, the heat generated in electronic devices needs to be dissipated to the surroundings.
Now, a team of researchers from the University of Illinois at Urbana-Champaign (UIUC) and the University of California, Berkeley (UC Berkeley) has developed a new cooling method that offers a substantial increase over conventional approaches in devices’ power per unit volume.
Tarek Gebrael, a UIUC Ph.D. student in mechanical engineering, explains that the existing solutions suffer from three shortcomings – first, they can be expensive and difficult to scale up. Second, conventional heat spreading approaches generally require that the heat spreader and a heat sink be attached on top of the electronics device. Unfortunately, in many cases, most of the heat is generated underneath the electronic devices, meaning that the cooling mechanism isn’t where it is needed the most.
And third, Gebrael explained, the heat spreaders can’t be installed directly on the surface of the electronics. They require a layer of “thermal interface material” sandwiched between them to ensure good contact. However, due to its poor heat transfer characteristics, that middle layer also introduces a negative impact on thermal performance.
Now, researchers have come up with a new solution to address all three of those problems. First, they used copper as a primary material, which is relatively inexpensive. They then made the copper coating that entirely “engulfs” the device, says Gebrael, “covering the top, the bottom, and the sides… a conformal coating that covers all the exposed surfaces” – so that no heat-producing regions are neglected. And finally, the new solution removes the need for a thermal interface material and a heat sink.
“In our study, we compared our coatings to standard heat sinking methods,” Gebrael says. “What we showed is that you can get very similar thermal performance, or even better performance, with the coatings compared to the heat sinks.”
Nevertheless, a device using the new solution is dramatically smaller than one using heat sinks, which are bulky. “And this translates to much higher power per unit volume. We were able to demonstrate a 740% increase in the power per unit volume.”
This makes a huge difference in the real world. Researchers are still investigating the coatings’ reliability and durability, which are critical to industry acceptance. The coatings can be used both in air and in water, the latter of which is needed for “immersion cooling” applications.
New electronics cooling tech enables 740% increase in power per unit volume
Source: Tambay News
0 Comments